Another way is to create parameters in Fluent for whatever you want to vary. For example, I wanted to vary the boundary conditions for an aerofoil simulation to change the angle of attack, e.g.
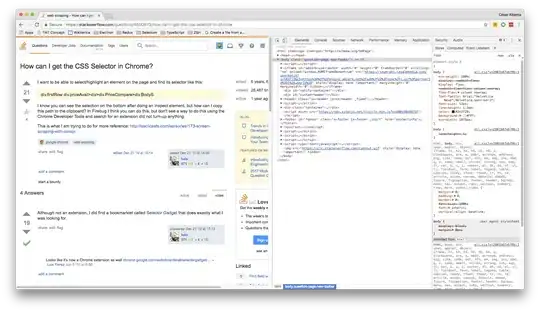
where blue arrows need to be set to different components to give different angles of attack, something like:
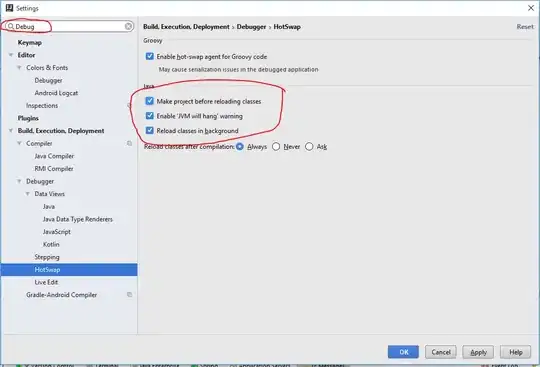
First make sure your case runs and gives sensible results setting the boundaries as numbers. Then, the two components of velocity in the boundary conditions can be set to parameters from the downwards arrow on the right, choose New input Parameter for each and give sensible names,

Here my two velocity components are Ux
and Uy
. Then go to the parametric tab, click Add Design Point a few times and export to a csv file,
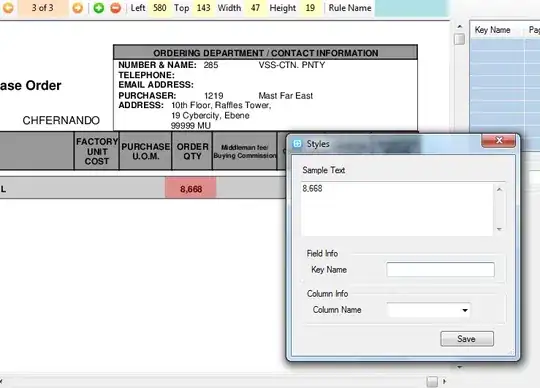
Then you can simply copy the range of points you want to run, overwriting values in the csv file and adding extra rows as needed.
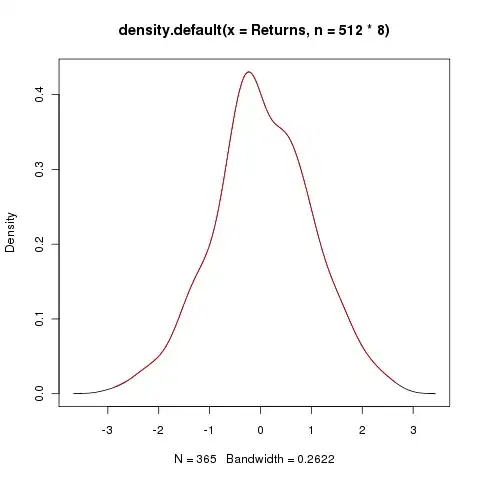
Then reimport this into Fluent. To get a useful output, here I wanted the drag/lift coefficient, you want to create a report item in the Report Definitions under Solution
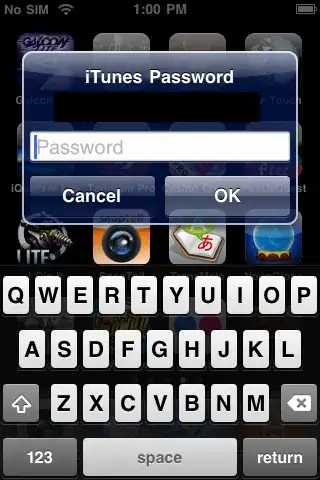
be sure to tick

so this appears on the Parametric study tab.
Then provided the individual case ran, the Update All
button should give the results of the parameter study. It's worth noting, in my case at least, reported drag and lift forces assume X=1 Y=0 and X=0 Y=1 respectively so may need some rotation base on the inflow angle...